リチウムイオン電池パック、カスタム開発のコツ(1/2 ページ)
電池で駆動する機器を設計する際、リチウムイオン電池パックとしては、市販のものを利用するケースが多いだろう。しかし、機器自体の量産規模によって、あるいは独自に安全機能の充実を図りたいといった場合には、カスタム仕様の電池パックを設計することも選択肢となり得る。本稿では、その際に知っておくべき知識やノウハウについてまとめる。
リチウムイオン電池を巡る動向
一般に、ノート型パソコン用の電池パックは、50Wh(ワット時)を超える電力量を蓄積できる。こうした大きなエネルギーを蓄える電池パックの安全性を動作条件内で保証するためには、電池パックの設計/製造および使用において細心の注意を払うことが求められる。
電池に関する専門知識を得ようと考える設計技術者はあまりいない。実際、そうした専門知識が必要とされる分野で働く技術者の数は少ない。ただし、電池パックが安全に動作することの確認や、ホストシステムが電池パックの動作を監視する仕組みを作ることは、電池で駆動する機器にかかわる技術者に必須の業務である。少なくとも、電池パックの仕様がどのように決まるのかということや、電池パックに必要とされる試験/検査などの内容、ならびに電池パックの動作を監視する手法については理解しておかなければならない。
リチウムイオン電池は、エネルギー容量が大きいことから、携帯型民生機器で使われる2次電池の主流を占めるようになった*1)。この種のリチウムイオン電池パックでは、安全性を確保するために、ヒューズやモニター回路、残量計、SMBusインターフェース、認証回路を内蔵するのが標準的なこととなっている。
業界標準のリチウムイオン電池セルは18650型である。18650型セルの大きさは単3型乾電池とほぼ同じ。この小さなセル1個だけを使う場合であっても、ヒューズやモニター回路などを装備した電池パックの形としてから電子機器に搭載しなければならない。
また、リチウムイオン電池セルの利用を考える際には、安定したサプライチェーンを有するベンダーの選定が不可欠である。近年のリコールの大量発生、工場の閉鎖、原料の不足といった事態が、リチウムイオン電池の入手を難しくしているからだ。さらに、輸送コストの増大、外国為替交換比率の悪化、リチウムイオン電池を搭載する製品分野の拡大(民生機器や電動工具、自転車など)、電池セルの価格上昇などが、確実なサプライチェーンの確保を最優先の項目に押し上げているとも言える。
電池パックのカスタム開発
リチウムイオン電池セルを初めて商品化したのは、ソニーである。1990年代始めのことだ。ソニーはパナソニックとともに、現在でも大手リチウムイオン電池メーカーの1つである。
生産数量が小規模から中規模で、コストの低減を重視する電子機器であれば、中国のベンダーが提供する電池パックが選択肢の1つとなる。中国には膨大な数の電池ベンダーがひしめいている。その多くは、大手企業ではなく、中小企業に分類できる。
ただし、価格だけを理由として電池パックを選択することはお勧めできない。それを採用するセットの品質を確保するために、電池パックの受け入れ検査のコストがかえって高くつきかねないからだ。また、市場に出荷されたセット製品で電池パックの不良が発生すれば、製造物責任を問われることになる。
量産規模が大きな製品では、カスタム仕様の電池パックを開発する予算を捻出できることが少なくない。量産規模が中規模程度でも、高い品質と大きな電力量が必要となる用途では、カスタムの電池パックを独自に開発することが選択肢となる。例を挙げると、医療機器がこのタイプの機器に当てはまる。
電池パックをカスタムで開発するには、電池パックの設計を実際に担う企業や電池セルベンダーなどからの協力が欠かせない。その際には、自社製品のさまざまな動作状況における電力負荷曲線や温度条件などが、協力企業に意思を伝えるための重要な道具となる。例えば、電動工具用電池の放電電流曲線には、切断または穿孔の作業に伴う高電流スパイクが現われる(図1)。電流スパイクの振幅と発生する期間は、ネジ止めなのか切断なのかといった具合に、作業の対象が何であるかによって異なる。
無線トランシーバ機器においては、通信中に電流スパイク(すなわち、瞬時的に流れる大電流)が生じるのにもかかわらず、ディスプレイなどの回路には一定レベルの電流を供給し続ける必要がある。想定される負荷曲線を電池パックの開発企業に示し、その要求を満たす試作品の提出を求めるべきだろう。
実際、機器によって要求事項はさまざまである。カスタム電池パックの設計/製造ベンダーである米Micro Power Electronics社でマーケティングマネジャを務めるRobin Tichy氏は、「医療分野では、電池パックのすべてを完全な充放電サイクルでテストする。加えて、顧客によっては、すべての電池パックが適切に組み立てられていること、十分な容量を備えていることの確認を求めてくる」と語る。要求がさまざまであるため、同社が特殊な仕様のテスターを独自に開発しなければならないケースもあるという。また、顧客からの要求レベルもさまざまである。例えば、適切に組み立てられていることのテストについては、「簡単な電圧試験だけを要求する顧客もいれば、抜き取り(サンプリング)試験だけでよいとする顧客もいる」(同氏)という。
安価な残量計ICを使う場合、あらかじめ個々の電池パックを充電しておき、それから放電するという作業を行って、電池パックを校正しておく必要がある。この校正作業は、電池パックの製造コスト/価格を押し上げる。そのため、「電池パックの組み立て後に充放電サイクルを必要としない残量計ICの採用も検討しておくべきだ」(Tichy氏)という。このタイプの残量計ICには、米Texas Instruments社の「Impedance Track」ファミリがある。残量計ICの価格そのものは高くつくものの、全体のコストで見た場合にどちらが高くなるかということについて検討すべきである。
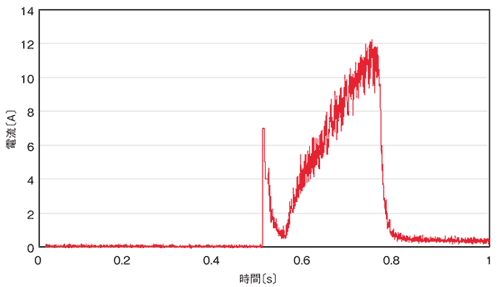
図1 電動工具における放電電流曲線 装置の設計者は、装置の電力の使用条件を電池の放電電流曲線で表すことになる。この曲線データは、電動工具(電動ドライバ)用電池パックの例である。実際にネジ止めを行う際に、大きな電流スパイクが放電電流曲線に生じている。ほかの電動工具であれば、切断や穿孔(せんこう)などに伴って大きな電流スパイクが生じる。
脚注
※1…Conner, Margery, “Portable power: Features abound, thanks to new battery chemistries,” EDN, Nov 22, 2007, p.46
Copyright © ITmedia, Inc. All Rights Reserved.